Tapping Screws type A, AB, B, BP
|
 |
Type A point: A thread forming screw for use in thin metal .015 to .050 thick. Used with drilled, punched or nested holes in sheet metal, resin impregnated plywood, and combinations of material. |
 |
Type AB point: A thread forming screw combining the locating point of Type A with thread size and pitch of Type B. Normal limitations of type B apply. |
 |
Type B point: A thread forming screw for use in heavier metal .050 to .200 thick. Larger root diameter with finer thread pitch for light and heavy sheet metal non - ferrous castings, plastics, impregnated plywood, combinations of materials, and other materials. |
 |
Type BP Point: Same as Type B but has a cone point for use where holes are slightly misaligned. |
 |
Decking Screws: Exterior screw for applications including decks, treated wood, arbors, fences and other applications that require a high degree of corrosion resistant. |
 |
Decking Screws 17: The addition of the type 17 point help the screw penatrate quickly in some of the hardest woods. |
 |
Partical Board Screws: Made with asymetrical threads that resists slippage and pull out. These superior holding power screws offer fast assembly in most particle board and wood applications. These screws are available in coarse and fine threads. |
Thread Cutting Screws Type F, D, T, BT, G, 1, 17, 23, 25
|
 |
Type F point: A thread cutting screw with machine screw thread with blunt tapered point, having multi - cutting edges and chip cavities. For heavy gauge sheet metal, aluminum, zinc and lead die castings, cast iron, brass and plastic. |
 |
Type 1 point: A thread cutting screw with single flute for general use. Produces a fine standard machine screw thread for field replacement. These are also known as a Type D thread cutting screw. |
 |
Type 23 point: A thread cutting screw in the fine thread series offering maximum thread cutting area and excellent chip clearing, with minimum tightening torques. These thread cutting screws are also known as a type T thread cutting screw. |
 |
Type 25 point: A thread cutting screw similar to type 23 point except with coarse Type B thread. For plastics and other soft materials with large chip clearing and cutting edges. These screws are also known as a type BT thread cutting screws |
 |
Type 17 point: A thread cutting screw for wood with a coarse tapping screw thread and a special long sharp point fluted to capture chips. Type 17 points can also be on Hi-Lo, deep root, deck screws and partical board screws. |
 |
Type BF Point: Thread cutting screw with type B threads and blunt taper point having multiple cutting edges and chip cavities. |
 |
Type G Point: Blunt die point with a single through slot to form two cutting edges. For same general use as type C but where less driving torque is required. |
Thread Forming Screws Type "TT", C, CA, PT trilobe for plastic
|
 |
Tri-Round: Type” TT” a thread forming screw in mostly coarse machine screw threads. It gives a further advantage of not producing chips verses a thread cutting screw in an untapped hole. Three vertexes perform a roll - forming process to form mating threads. These can be used to eliminate the tapping of unthreaded holes. Much better thread forming than Type C or CA, and drives with less torque. |
 |
Type C point: Is a thread forming screw with either coarse or fine pitch machine screw thread and blunt tapered point. Eliminates chips and permits replacement with standard screw in the field. Higher driving torque required. Type C points are usable in heavy sheet metal and die castings. |
 |
Type CA point: A thread forming screw with either coarse or fine pitch machine screw thread. Same as Type C except with a Gimlet point. The locating point works better than Type C where holes between two adjoining pieces of sheet metal may be somewhat misaligned. |
 |
Type PT Thread Forming: A 48' or 60' thread feature reduces displacement of plastic for less internal stress and less tendency to fracture bosses. Better drive/ strip ratio and strip torque are obtained when compared with conventional Type B tapping screws. A good choice for plastic applications. |
 |
Type Hi-Lo Point: A Hi-Lo is a dual lead thread formong screw for use in plastic, nylon, wood, or other low density materials. The thread design reduces driving torque, improves drive to strip out torque and lessons the risk of cracking the application. |
 |
Low Root: Low root thread is designed in sharp points or blunt points. The wide spaced thread forming screw is designed for plastic applications due to the increase in the drive to strip out ratio and reduced cracking of the boss. There are many variations in this catagory and per print parts. This catagory of screws comes in blunt points as well as the addition of a thread cutting feature. Please contact your Eagle salesperson to assist you in this category of fasteners. |
Self Drilling & Self Piercing Screws
|
 |
Self-Piercing: Produces more secure sheet metal assemblies. This fastener can be used as self-drilling screw or used to drive thru pre-punched holes or no holes in light gauge sheet metal. The twin lead drills straight thru sheet metal at peak speed. Perfectly mated threads increase strip and back out pressures. These are also know as a needle point, speed points or sprint points. |
 |
Self-Drilling: Comes with drilling points that will drill through metal, wood, and plastic applications. Eliminates all hole preparation, therefore reducing the in-place fastener cost. No punching, drilling or tapping required. There are several points styles including type 2, 3, 4 & 5 drill points depending on the application and size. |
Point Styles for Machine Screws and Tapping Screws
|
 |
Header Point: One of the least expensive pointing operations applied at the time of heading. This operation provides an end chamfer starting with a diameter smaller than the root diameter of the thread. The minimum reduction of the point is approximately 10% below the maximum minor diameter with an included angle of 40 to 50. |
 |
Dog Point: A straight pointed section reduced in diameter slightly below the root diameter of the thread, usually extending in length about two-thirds the diameter of the thread. Recommended for ease in starting, to insure against stripping fine threaded products, and to increase efficiency along production lines. |
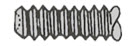 |
Rolled Point: An efficient method of producing pointed long studs or long screws with an end chamfer similar to the Die Point. The last thread and a half is slightly cupped by the thread roll-over operation. |
 |
Pinch Point (Rounded): An inexpensive method of applying a 40°, 60° or 90° lead-in point having a slightly rounded contour but with pinch-off marks on its surface. Used for aligning several sheets or assembling several parts requiring pilot action. |
 |
Nail Point (Pinched): Usually supplied with an approximate 45° included angle having a sharp point and slightly squared surface. Used for impinging or locking against wood or other soft material. Other degrees of included angle and sharpness also available. |
 |
Cupped Point: A special cup section supplied on the end of the threaded member having a depression in the end to reduce the area in contact with the surface which increases its holding and locking power under pressure. |
 |
Round Point: A dome-like rounded surface applied to the end of a threaded member in order to offer pressure without disfigurement. Used for adjusting members where friction without cutting action is desirable. |
 |
Cone Point: A precision forming operation to provide any required included angle. Offers a smooth surface, accurate length, and a sharp point which can be produced to any desired contour to fit your particular requirements. |
 |
Type U Drive Point: A thread forming screw with high Helix thread for driving or hammering into sheet metal, castings, fiber or plastics for permanent, quick assemblies. |